-
新闻资讯
- 激光应用
- 行业资讯
- 久恒风采
销售热线:
电话:0577-66871553
邮箱:sale@highlaser.cn
1688网店:
总公司地址:浙江省瑞安市阁巷新区东二路138号32幢
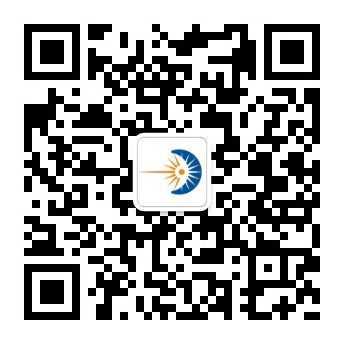
温度场模拟与表征的研究现状
王旭, 于月光, 黄恩泽, 杜开平, 李正秋
东北大学材料科学与工程学院
北京矿冶科技集团有限公司
北京市工业部件表面强化与修复工程技术研究中心
摘要: 熔池内存在传质、 传热、 对流及气-液-固界面间的反应, 熔覆过程中温度场的变化对熔覆层组织和性能产生重要影响, 正确解析这一复杂物理冶金过程, 对激光技术发展有重要指导作用。本文回顾了近年国内外激光熔覆温度场的模拟研究进展, 重点评述了激光加工温度场从数学分析到数值模拟的研究历程, 并针对这一领域今后的发展提出了一些看法。
0引言
激光熔覆技术自诞生以来, 在工业中已获得了大量应用。目前, 国际上关于激光熔覆的研究热点主要集中于如表 1 所示的领域。不难看出,激光加工的温度场和流场的模拟与表征依然是各国机构关注的重点之一。
1 激光熔覆温度场的研究
1.1激光熔覆温度场的影响因素
激光熔覆过程中, 温度场的影响众多, 如送粉速率、 熔覆层厚度、 光斑直径、 扫描速度等,用实验的方法来研究热机制或者使用设备来检测熔池温度、 涂层应力分布等十分困难, 且成本非常惊人, 送粉法激光熔覆工艺原理如图 1 所示。随着计算机技术在数值模拟领域的广泛应用,为研究熔覆过程中的复杂物理化学现象提供有效的手段, 目前激光快速成型领域内温度场模拟工作的软件数量众多, 使用较为普遍的有 ansys、msc.marc、 abaqus/standard 等软件。
图 1 送粉法激光熔覆示意图
激光熔覆热源的选取对熔覆层的质量有很大的影响。在热源热输入的分析中, 高斯分布热源模型和双椭圆功率密度模型应用最为广泛。其中,高斯分布热源模型如下:设激光的辐照功率为 p,基模高斯光束的半径为 ω, 定义η为基模高斯光束的占有系数, 则tem00 及tem10 两种理想模式按不同强度比例进行叠加的光束在 (x, y) 平面的功率密度分布函数可表示为:
选择不同的 η(通常取 η=0、0.5、0.75),将得到不同形式的光束。在进行实际模拟计算时,常假设激光光束的能量是恒定的, 并且激光光源采用近似高斯分布(即取 η=0)。
激光熔覆过程中, 各种表面之间存在着复杂的相互作用, 其中温度的变化是基础, 热变形的同时引起显微组织的相变抗力, 组织相变又产生了相变潜热作用于温度场, 相互作用关系如图 2所示。长期以来, 激光能量的热作用理论研究多采用数学分析和数值模拟方法进行, 并经历了从一维到三维, 从导热控制的温度场到对流控制的温度场, 从仅计算熔池到综合考虑粉末与激光、基体相互作用等一系列简单到复杂的过程。
图2 熔覆温度、 应力应变及显微组织的关系
1.2激光熔覆温度场的数学分析
激光熔覆温度场的模拟与表征有利于推导涂层组织结构的演变规律, 激光加热的数学模型,在研究初期多采用移动光源条件下的导热控制模型,即在基体内部能量方程只考虑扩散不考虑对流,主要是因为基体热物性参数是重要影响因素。早期模型受到计算手段所限, 以二维的解析求解为主。
jaeger推导了移动热源扫描无限大表面时的 温 度 分 布 解 析 方 程, rosenthal[7]、 carslaw 和jaeger 发展了该移动热源理论, 对不同形状光斑在半无限大基体上的热作用给出了确定解。cline和 anthony假设几何尺度无限大、 热物性参数不随温度变化, 将冷却速率、 熔化深度、 扫描速度和激光功率联系起来, 用格林函数法求解了导热方程。但当熔池深度与基体厚度相当时, 基体的半无限大假设就不再成立了。为解决这一问题,研究者们又开始发展有限厚度基体的求解方法。pittaway求解了绝热薄盘在静止和移动圆形高斯光束下的温度场, kuang采用同种热源求解了有限深度、 无限宽度绝热体的线性热影响的问题。虽然解析意义明确, 但应用环境受到限制,且要多重假设甚至使结果偏离实际问题, 而数值模拟在一定程度上可以有效的弥补上述的缺陷。
1.3温度场的模型建立与数值模拟
kar 和 mazumder 提出了一维传导模型来确定合金的组成和冷却过程。hoadley 和 rappaz提出了一个二维模型来计算激光熔覆过程中稳态温度, 具有一定的代表性, 给出了基体温度场的准稳态数值模型, 计算中考虑了液态熔池的变化和气液自由表面的形状及位置, 为了简化模型,认为基体熔化极少并采用激光的线能量形式, 从而得到了激光功率、 扫描速度和修复层厚度的近似线性关系。han 等人求解了二维流体和能量方程, 预测了激光熔覆过程中熔池的温度分布和几何形状。cho 和 pirch等人发表了同轴送粉的三维稳态有限元模型。采用自洽的方法对温度场和涂层形状进行了数值计算。利用得到的温度梯度和冷却速率对涂层凝固组织进行预测。jendrzejewski在基体x10cr13上熔覆钴基合金,讨论了预热温度对修复层温度场和应力场的影响,对其温度特性采用线性近似, 经预热后, 基体修复层其热应力值由 1800mpa 降为 900mpa, 且得到了无裂纹的修复层。toyserkani等人提出了一种同轴送粉的三维瞬态有限元模型, 涂层为多层结构,其宽度和高度由前一层面积和粉末质量决定, 该模型忽略了表面张力和重力对涂层形状的影响。he等人研究了h13钢激光熔覆过程中熔池温度和流体流动的三维数值模型,采用水平集的方法模拟熔池。美国南方卫理工会大学激光辅助制造中心 kovacevic等人用 ansys 建立了有限元模型,如图 3所示。研究了正负离焦情况下,熔池温度分布和冷却速率的规律,通过与高斯激光束比较发现空心激光束(离焦)有效的防止熔池中心过热的情况,但该模型未考虑粉末输入到熔池时产生的影响。
图 3 熔池温度分布 ansys 有限元模型
加拿大航空航天制造中心 dubourg 等人研究了不锈钢上激光熔覆 co-wc的参数(扫描速度、送粉率、离焦率和搭接率) 对涂层几何形状的影响及对 wc 含量的影响,如图 4 所示。该研究采用了田口实验方法,结果表明随着送粉率、扫描速度和离焦距离的减小导致涂层稀释率升高,致wc 含量明显降低,且该研究还报道了单道与多道涂层的尺寸与 wc 含量之间没有直接关系,但该研究没有考虑 wc 的热力学转变和分解的情况。
图 4激光熔覆参数(扫描速度、送粉率、离焦率和搭接率)
对涂层几何形状的影响
1.4工艺与涂层几何特征的表征
ansari等人通过回归分析研究了单道熔覆中主要工艺参数(扫描速度、 送粉率、激光功率)与熔覆形貌(宽度、高度、深度、稀释率、润湿角)之间的关系。safonov等人提出了一种熔体运动和表面形状的近似计算方法, 以确定熔体的运动速度和表面张力的作用情况。对于铁合金熔池宽度×厚度为2×0.2mm,熔体在表层以1~3m/s的速度移动,计算了中央和边缘部分的温度差为500℃。nabhani等人将 ti-6al-4v粉末合金用激光熔覆沉积在同质基体上,研究了工艺参数(扫描速度、送粉率、激光功率) 对单道涂层几何特性的影响。erfanmanesh等人采用回归法分析了单道激光熔覆参数与涂层几何特征之间的关系,得到在 aisi321 不锈钢表面激光熔覆 wc-12co的最佳工艺参数, 制备出低孔隙率高质量的涂层,其中搭接率和激光功率对涂层宽度的影响规律如图 5 所示。
图 5 单层多道激光熔覆功率和搭接率与涂层宽度之间的关系
shi 等人利用能量和质量守恒定律,根据单位熔池体积能量密度, 研究工艺参数(激光功率、扫描速度、 送粉率) 和几何特征(宽度、 高度和截面积)之间的关系, 并通过实验结果验证模型。ocelik 等人提出了单层多道表面波形和涂层高度的关系模型, 并对模型进行了验证, 但未考虑送粉率对其产生的影响。suryakumar等人建立了单层多道、 单道多层熔覆模型, 如图 6 所示,并针对不同工艺路径对该模型进行了验证和优化。
图 6 单道多层熔覆时, 熔池温度和深度随功率变化的曲线:(a) 熔池温度;(b) 熔池深度
2结论
综上所述,国外众多学者在激光熔覆熔池温度场的数学物理模型中主要存在着如下共同点:首先,假设熔覆的过程为稳态或瞬态,工件为某一方向无限大或有限尺寸;其次,材料的热物性参数是温度的分段线性函数,而作用力仅考虑熔池的表面张力和浮力,在导热控制的温度场上加入了对流项, 且对流项为层流;第三,熔池表面是平面或可变形的自由表面。应用这些比较符合实际的数学物理模型,不仅完成了熔池内传热、传质的计算机二维、三维数值模拟,而且还针对激光加工的工艺参数(热源模型、光斑尺寸、 激光功率、扫描速度等)对熔池形貌、冷却速度、温度梯度、组织结构之间的耦合性开展了大量的研究,得到了许多有价值的结论。但前人建立的模型仍存在以下有待探究的问题:
(1) 模型在湍流对熔池冶金动力学过程的影响方面有待于进一步探究,这种影响对于解释熔池流体流动复杂性是至关重要的;
(2) 对固-液共存的流场分析进行一定程度的简化,而当熔覆对象为凝固温度区间较宽的合金涂层时,需进一步研究流场的流动对温度场分布的影响;
(3) 符合激光熔覆熔池特点的边界条件被提前锁定,而流体流动的驱动力不仅仅有表面张力和浮力,还有气体的压力,在送粉法激光熔覆过程中还有粉末对熔池表面的冲击力,这方面的研究也不容忽视;
(4) 可以通过测定不同工艺条件下激光熔覆层中熔覆层枝晶二次臂间距, 计算非平衡凝固过程的熔体温度梯度,并结合实验验证计算结果的准确性, 可用于修正三维瞬态温度场、流场数学物理模型;
(5) 通过研究熔池气-液-固体界面冶金反应机理,计算熔池中合金元素烧损量, 为激光熔覆质场数值模拟提供精确的边界条件和热物性参数;
(6) 随着大尺寸厚涂层零件的激光熔覆,以及快速激光熔覆的发展,往往用到多道多层的熔覆工艺,这一过程温度场的计算与模拟将变得异常复杂, 这一方向的研究尤为重要。
本文发表在《热喷涂技术》第11卷第四期(总第42期)2019年12月:p10-p15。