-
新闻资讯
- 激光应用
- 行业资讯
- 久恒风采
销售热线:
电话:0577-66871553
邮箱:sale@highlaser.cn
1688网店:
总公司地址:浙江省瑞安市阁巷新区东二路138号32幢
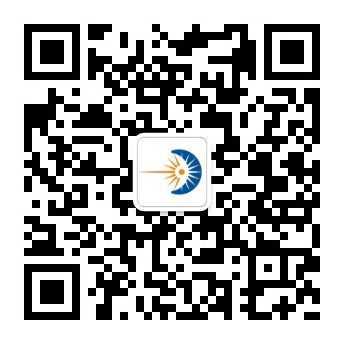
摘要
如今,客户的需求是动态变化的,行业正朝着定制化的终端用户产品的制造方向发展,市场的波动非常难以预测。这要求生产行业转向瞬时产品开发战略,即在最短的交货时间内交付产品,而不损害质量和准确性。直接金属沉积就是这样一种不断发展的增材制造技术,它的应用范围从快速成型到实时工业部件的生产。
此外,该工艺非常适合即时制造,即按需生产零件,同时提供降低成本、能源消耗和碳足迹的潜力。这种先进制造技术的发展大大减少了制造约束,大大提高了产品的多功能性。本文从粉末床融合和金属直接沉积两方面对金属增材制造(mam)技术的发展、现状和挑战进行了综述。此外,本文还对金属增材制造的各种变体及其工艺机理、优缺点和应用进行了探讨。最后采用时间成本三角法分析了工艺的效率,并对其机械性能进行了综合比较。该检讨将增进对mam的基本认识,从而扩大研究和发展的范围。
1.介绍
在20世纪80年代早期,第一种以逐层制造技术创建三维物体的形式被开发出来,这被称为快速原型(rp)。固体、液体和粉末是主要用于快速成型的三种原材料的变体。随着材料用途的扩大,am工艺的多样化应用导致了金属零件的直接制造,同时满足了客户在几何精度和物理机械性能方面的要求。高精度、高精度的复杂零件几何形状的加工是定制零件生产的关键。为了解决这一问题,一种名为金属增材制造(mam)的新兴技术被广泛应用,为制造领域带来了广泛的新可能性。此外,最近在建模科学,制造和材料加工导致am的重点从快速成型转向直接生产金属零件。
20世纪80年代初,carldeckard开发并申请专利的选择性激光烧结(sls)技术,可以打印出使用多种材料的物体,如塑料、玻璃、陶瓷,甚至金属,被称为直接金属激光烧结。这使得它成为原型和最终产品生产的流行过程。在20世纪90年代后期,激光烧结技术被广泛应用于直接制造金属零件。首先,在1994年,光电系统公司(eos)展示了他们的eosint 160机器原型,它基于直接金属激光烧结技术(dmls)操作。后来,eos公司将eosint 250机商业化投放市场,实现了金属零件的快速生产。根据astm, mam被定义为“一种从3d cad模型数据,通常以一层一层的方式制造组件的过程,而不是减材制造过程”。mam工艺是一种无工具的制造方法,具有多种多样的零件生产、最小的人机交互和减少设计周期等显著优势。因此,该工艺发展成为工业标准金属组件生产的综合研究领域。
结合金属沉积(bmd)挤出机
bmd是一种以挤压为基础的金属am工艺,其中金属组件是由粉末填充的热塑性介质挤压而成。bmd技术使用stl文件和本地cad文件作为输入。一旦文件被处理,该部件是用金属粉末和粘合剂(蜡和聚合物粘合剂)制备的加热金属棒挤压而成。一旦印刷,粘合剂被去除,通过粘合过程,然后烧结,导致金属颗粒致密。该工艺使用两种挤出机,一种挤出金属棒作为实际部件,另一种挤出陶瓷界面介质棒,用于在构建腔内分离多个部件,构建支撑等。微波辅助烧结工艺使零件的烧结速度更快。bmd的优点是在印刷过程中不使用任何热源,因此不会产生残余应力。印刷之后是在熔炉中烧结,涉及缓慢均匀加热和最小的应力产生。此外,支架结构拆卸非常容易,不需要加工。bmd是一个比bj更快的过程。另一方面,该工艺不会产生全密度零件,需要后处理烧结来提高强度。desktop metal将bmd商业化(上图)。
金属增材制造具有制造复杂结构件的高能力,这是很难或甚至不可能通过传统制造技术制造的。mam的独特之处在于,它能够直接从3d计算机辅助设计(cad)模型制造定制零件,而不需要昂贵的模具系统。此外,mam可以根据需求生产零件,同时减少备件的库存。除此之外,关键的或过时的组件的交货时间也大大减少使用mam。
值得注意的是,mam的显著亮点是单位零件成本,与传统制造技术相比,它几乎是恒定的。几乎每一种传统的制造方法,如铸造、成形等,在单位零件分析成本上变得更便宜。但是,对于小批量生产来说,它们执行起来非常昂贵。这主要是由于制造一个单位零件所需的管理费用和成本之间的差异。在mam过程中,几乎没有间接成本,因为它优化了高度先进的自动化技术。mam是一种成本效益高的技术,它更适合制造低、中批量生产的零件。基于这些原因,mam被广泛接受,并被公认为航空航天、汽车、医疗和能源领域高性能部件设计和制造的新范例。
这篇综述文章的主要目的有两个方面。第一个是提供mam技术的发展,特别是在固体、液体、线材和粉末技术的原理和功能方面。此外,还讨论了各工艺的机械性能、工艺潜力和质量方面的问题。第二步是根据时间-成本-质量三角形来比较各种工艺参数。
2.mam的历史与演变
am工艺在快速零件生产中提供了显著的优势,也提供了无与伦比的设计自由度,可以用多种可用材料制造单个组件或多个组件。terry wohlers和tim gornet简要介绍了mam工艺的发展,其中立体光刻(sl)商业化用于生产工业部件,其中该技术使用激光源有效地固化uv光敏液体聚合物薄层,主要用于原型制造。sla-1是世界上第一个由3d系统在1987年年开发和商业化的立体光刻系统。后来,许多组织发展了他们的立体光刻系统,并将其引入商业市场。eos和3d系统在其他组织的立体光刻系统的发展中发挥了主导作用。stereos 400是在20世纪90年代由eos[5]开发和销售的。quadrax在此期间还推出了mark 1000 sl系统,该系统使用可见光树脂聚合物材料来制造原型部件。
金属沉积工艺制备的不同厚度泡沫镍样品的sem图像:(a)镍层较薄;(b)较厚的镍层
金属沉积型多孔金属是通过在开孔聚合物泡沫上沉积原子金属,然后消除聚合物和烧结来创建的。这些金属的主要特征包括连接孔、高孔隙率和三维网状结构。多孔材料是一类非常重要的多孔金属材料,是一种性能优良的新型功能结构一体化材料。在一定条件下使用,其优点是密度低、孔隙率高、比表面积大、孔隙连通性好、结构均匀,这是其他类型的多孔金属难以达到的。但这一特性也对金属沉积型多孔金属的强度产生了一定的限制。这些材料首先在20世纪70年代被制造和利用,然后,在80年代,它们被迅速开发用于各种各样的应用和需求。目前,许多国家都在大规模生产这些多孔材料,镍和铜泡沫产品通常是通过电沉积工艺生产的。这种金属泡沫如上图所示。
金属零件的调质技术是在20世纪90年代初发展起来的。第一步是eos组织与electrolux研发公司达成合作协议,共同开发dmls技术。这次合作在eosint m160的商业化中达到了顶峰,这是第一个直接用于金属组件的增材制造。后来,三种新的am技术,包括stratasys的熔融沉积建模(fdm)、cubital的固体地面固化(sgc)和helisys的层压物体制造(lom),在1991年被商业化。fdm工艺以长丝的形式挤出热塑性材料,从而以一层一层的方式生产零件。sgc是一种使用液体光致聚合物构建3d结构的过程,这与立体光刻技术相似,通常被称为“士兵”。lom技术通过使用数字引导激光源将薄板材料或金属箔层绑定在一起,以制造三维金属零件。
dtm现在是3d系统的一部分,solidform系统在1992年引入了sls。该技术利用激光束作为热源,将粉末材料熔化。1993年,麻省理工学院开发了直接铸壳(dspc)技术并获得专利,该技术也被soligen technologies商业化。此外,在这个时期,denken的sl推出了固态激光系统。eos于1994年展示了其原型机eosint m160,其功能基于dlms技术。后来,eos组织在1995年推出了eosint m25o系统,该系统具有制造金属部件的能力。startasys和ibm watson研究中心在1996年开发了这台生成机,它利用材料挤压过程的原理来制造定制的部件。此外,在此期间,z-corp推出了z402 3d打印机,该打印机使用淀粉和石膏基粉末材料和水基液体粘合剂制作3d模型。一个名为“aeromet”的组织成立于1997年,开发了一种激光增材制造系统,通过使用高功率激光源来加工各种粉末材料(特别是粉末钛合金)。1998年,美国桑迪亚国家实验室开发了一种基于金属粉末的技术,称为激光工程净整形(lens),该技术后来被“optomec”商业化。optomec公司于1998年推出了基于粉末-激光相互作用的am系统,该系统采用粉末注入激光能量沉积技术。后来,像trumpf和dmg这样的商业制造商在接下来的20年里在ded技术的开发中发挥了主导作用。
后来,1999年,总部位于德国的roders公司推出了可控金属堆焊(cmb)机器,这是由德国fraunhofer研究所开发的。此外,在此期间,extrude hone组织(现在的ex one)开发并商业化了pro-metal快速模具系统rts-300,该系统主要用于制造金属部件和昂贵的工具。2001年,fockele 和schwarze一家德国公司在fraunhofer研究所开发了以钢粉为基础的选择性激光熔化系统。此外,concept laser公司开发了激光固化技术,以最小的材料浪费制造3d组件。此外,瑞典的arcam公司开发并商业化了电子束粉末床融合技术,该技术使用高功率电子束源来制造定制的金属部件。2003年,通快将粉末床熔合(pbf)技术商业化,利用激光能量直接熔合金属合金。在同一时期,索尼精密技术,一家美国公司,引进立体光刻技术在快速零件生产。后来,solidscape引入了t612系统,该系统主要用于熔模铸造工艺中制造蜡模。
eos在2006年推出了eosintm270机器,有能力制造钴铬粉末材料为基础的部件。在那之后,一个名为norsk titanium的组织在2007年开发了一种快速等离子体沉积技术(rpd),这是一种从传统等离子弧焊演变而来的am技术的改进形式。这种rpd技术主要应用于飞机和航天工业。在此期间,arcam和eos分别向美国市场推出了a2电子束熔炼(ebm)机和formiga p100激光烧结系统。后来,“objet geometries”在2008年推出了基于多喷射矩阵技术的多材料connex500 3d打印机。此外,在同一时期,mtt在英国2008年的一次活动中商业化了选择性激光熔化机(slm), slm 250-300。后来,eos和cookson贵金属公司开发了eos- m2012年推出系列机器,采用贵金属合金制作首饰。此后,在2015年初,许多上市am公司的市值明显下降。尽管如此,以金属为基础的pbf系统在航空、能源、天然气和石油行业仍然表现强劲。
desktop metal和惠普于2016年进入商业市场,并将金属粘结剂喷射技术(bjt)商业化。金属bjt系统于2019年安装在测试客户阶段。同时,在这段时间内,ge航空意识到了pbf-eb的潜在潜力,并投资了更多的系统来制造定制的飞机部件。在2020年,珠宝和装饰领域已经结合了am技术,pbf-lb,以经济的角度制造定制珠宝设计。此外,奥地利的tu graz公司引入了一种新的mam技术,称为基于led的金属增材制造,帮助解决了两个主要的问题,即大批量金属组件生产的时间消耗和组件的手动返工。这些问题通过采用led光源的金属粉末靶熔化技术得到解决。图1清楚地说明了上述mam过程的历史和演变。
图1 mam过程的历史与发展
3.mam技术综述
如前所述,客户对产品的需求在产品质量、产品尺寸、产品形状、产品制造交货期等方面都有所增加。客户的关键要求是在最短的制造时间内提供高质量的定制产品。这导致了am的快速发展这项技术后来演变成了mam。根据原料的不同,mam分为液态am、固态am、线状am和粉状am四种,如图2所示。表1比较了mam过程的性质、优势、机制和独特特征。
图2 基于原料的mam工艺分类
表1 mam过程的过程性质比较
4.工艺参数及机械性能比较
如前所述,要生产的产品需要考虑许多关键参数。它包括产品尺寸、产品形状、产品几何形状和产品材质。在所有的制造行业中,在产品制造开始之前,过程的潜力或能力都被清楚地详细地研究过。这些制造过程本质上是动态的,因此有必要根据产品特性进行优化。同样,它也在mam工业中进行。所有的mam过程都有其自身隐藏的潜能或能力,因此有必要了解每个过程的潜能。
4.1 time-cost-quality三角形
为了清楚地了解每个金属添加剂工艺的潜在潜力,首选时间-成本-质量三角,即项目管理三角,来分析和比较每个工艺的能力,如图3所示。根据每种工艺的质量特征、零件成型率和微观结构特征对其进行比较是非常必要的。此外,很难在单个图表中比较所有特征,必须在这些特征之间进行划分。表2比较了商用am系统的构建特征,而表3比较了使用am技术制造的材料的物理机械性能。
图3 时间成本质量三角
表2 mam过程构建特性的比较
表3 比较了使用am技术制备的材料的物理机械性能。
4.1.1 质量
每个制造行业的主要目标是通过降低生产成本来制造出高质量的产品。质量的定义有很多种,但简单地说,它就是顾客的满意或需求。详细的产品或零件规格数据,包括尺寸精度,表面质量,材料和机械特性是客户获得的主要关键因素。
4.1.1.1 表面质量
通常,采用mam技术制造的产品或零件具有颗粒状方面结构,这是由于零件外表面存在未结合的熔融颗粒。大多数情况下,粉末床基工艺的平均表面粗糙度在15毫米以下。与未进行后处理的sls和dmls相比,采用sls和dmls进行后处理的零件具有更好的表面光洁度。因为,ebm工艺算法粗糙度范围在25和35 mm之间,而ded技术产生一个更光滑的表面,ra值在10和25 mm之间。
4.1.1.2 尺寸精度
使用sla技术加工的零件尺寸精度为±0.15%,下限值为±0.01 mm。sls是一种精密加工工艺,常用于制造尺寸精度为±0.3%、下限为0.3 mm的复杂几何零件。此外,sls、dmls和slm技术制造长度为100 mm的最小尺寸误差小于0.1 mm的零件。sla制造精度小于1000cm的零件3 而sls生产的零件精度高,>1000厘米3 建立体积。
材料喷射是最精确的3d打印工艺,尺寸公差为±0.1%。此外,对于高温应用材料,特别是钛合金,ebm的尺寸精度是粉末基工艺的一半。但是,在高温应用材料上,激光成形工艺的尺寸精度较差。
4.1.2 时间
它仅仅意味着每道工序的生产速度或mam技术的建立速度。这种生产速度因物理材料特性、机器制造速度、能力和其他杂项因素而有很大差异。此外,这些都是影响交货时间的主要关键因素。
基于粉末的mam技术,如sls(120-125cm3/hr)和dmls(100-120 cm3/hr)的累积速率较slm(达113 cm) cm3/hr)。与slm过程相似,dmd(50-110 cm3/hr)及lam(16-250 cm3/hr),具有较高的施工速度,可制作无孔件。dmls和sls工艺具有相似的构建率,需要后处理处理来实现几乎完全致密的部件。ebm和ded技术是一种不需要特殊精加工就能快速制造零件的技术。
4.1.3 成本
制造产品的成本取决于机器运行成本、机器小时率、原材料成本和其他消耗品成本。制造时间也会影响产品成本,它根据工艺和机器能力的性质而有很大的不同。一般来说,该产品是用中等体积的建筑腔体制造的,粉基是最便宜的,而ebm和ded是最昂贵的。
5.总结
主要观察结果总结如下:
多年来,该工艺扩展到各种材料,包括金属、合金、陶瓷和聚合物。增材制造被商业化为流行的技术,如选择性激光熔化、熔融沉积建模和电子束熔化,这些技术在汽车、航空航天、生物医学和建筑等各个行业都得到了应用。包括eos、pom组织、stratasys、ibm、hp、aeromet、hellisys和fraunhofer在内的先锋公司进一步开发和商业化了am流程。
金属增材制造的广泛应用为制造领域带来了广泛的新可能性。此外,最近在建模科学、制造和材料加工方面的进步导致了am的重点从快速原型到直接生产金属部件的转变。mam根据原材料分为四大类,即液态基、固态基、线状基和固态基。mam工艺的几个商业变种被开发出来,发现了新的应用,如修理和重做关键和昂贵的零件。此外,mam工艺生产的部件具有相对类似于锻造和铸造的物理机械。
结果表明,工艺参数和mam工艺类型对沉积材料的机械性能有显著影响。与sls、ebm和dmls相比,ded生成的表面具有更好的算法粗糙度。另一方面,sls和dmls比slm、lam和ded的构建速度更快。此外,在采用pbf工艺的情况下,产品的制造成本也较低。然而,据观察,ebm和ded技术制造的产品具有较高的产品开发成本。
6.结论
本文对金属增材制造的主要工艺进行了详细的描述,并对金属增材制造工艺的发展进行了图解和详细的说明,如线材增材制造工艺、粘结剂喷射工艺、粉末床熔接法和粉末直接能量沉积法。此外,这些技术根据所使用的原料分类,它们是液体基am,固体基am,线基am,粉末基am和直接能量沉积基am。对于每一种am技术,不同的工艺参数被比较在不同的材料应用。此外,本文还简要介绍了各种am技术在不同材料上的应用和机械性能。在回顾各种mam过程时,可以得出以下结论:
•与液态金属3d打印工艺相比,固态成形工艺可以生产复杂的几何零件。
•基于固体的mam工艺,如lom和uam,具有生产表面粗糙度为14µm的稳健设计的能力。
•线材激光增材制造与其他线材am工艺相比具有更高的延伸率。
•基于粉末的mam工艺能够以更快的构建速度和更低的产品成本生产组件。这使得基于粉末的工艺广泛地用于制造和重做关键的和昂贵的部件。
来源:review on the evolution and technology of state-of-the-art metaladditive manufacturing processes,materialstoday, doi.org/10.1016/j.matpr.2021.02.567
参考文献:c. deckard, “method and apparatus for producing parts by selectivesintering,” in, u.s. patent (oct. 1986).,“background toadditive manufacturing.”https://www.metal-am.com/introduction-to-metal-additive-manufacturing-and-3d-printing/background-to-additive-manufacturing/(accessed dec. 10, 2020).